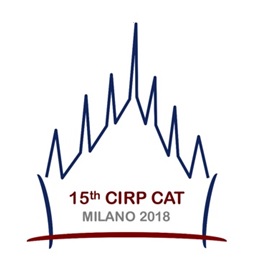
Robust Design is a well-acknowledged design approach that strives for designing products, devices and production equipment so that their performance and function is insensitive to the variability and uncertainty inherent in manufacturing, assembly, and use processes. Focusing on systematic efforts during product and process development, Robust Design significantly widens the scope of uncertainty management and quality control practices and offers an enormous potential in terms of reducing quality issues, scrap, or delayed product launches.
At the same time, it is largely unclear how corresponding design approaches can benefit the indispensable tolerancing and geometrical variations management tasks in order to systematically and successfully account for variability and uncertainty in product and process development. Therefore, it is relevant the need to discuss novel approaches and tools that allow for a coherent consideration of variability and uncertainty throughout the whole process of design and geometry assurance, and that enable the minimization of variations as well as the continuous monitoring and optimization of the resulting product performance by means of suitable verification and validation activities.
It is well established that additive manufacturing (AM) is a historical breakthrough in manufacturing and deeply impacts the overall design and manufacturing process chain as well as the entire life cycle of a product. The greater benefits of AM come from the fact that by adding material point-to-point and layer-by-layer, it is possible to control both the shape and material complexity of a product. This "complexity for free" requires alterations to current methods to describe and communicate complex design. This need is particularly true and well recognized with respect to the development of methods to tolerance complex freeform surfaces; to communicate and tolerance heterogeneous materials and internal features; and to verify dimensioning and tolerancing requirements of the additively manufactured parts.
Nowadays, many manufacturing processes are available capable of manufacturing components whose size is well below 1 mm. However, the correct definition and inspection of such components is still a difficult task: at micro-scale level the geometry of the part influences the functionality not only in terms of mating and movement. Then, the question arises whether or not the current GD&T and GPS practices are still adequate. Therefore, new techniques for tolerance analysis, synthesis, and allocation are needed. Verification also needs to be harmonized with the new tolerancing techniques, but in this field an additional challenge is present. In general, inspection systems for micro metrology are non-contact measuring systems. A complete infrastructure guaranteeing the traceability of non-contact micro-measuring systems like quantitative microscopes still needs to be developed and implemented, including instruments calibration and verification, and measurement uncertainty estimation.